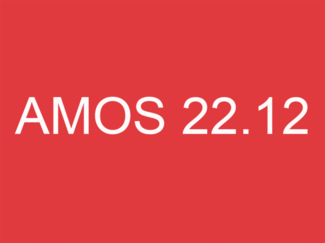
AMOS 22.12 was recently published by Swiss-AS. Here are a few highlights:
Performance
The Cloud Readiness of AMOS has been improved by eliminating the 30 biggest roundtrip eaters. A lot of effort has been dedicated to optimise 26 user transactions out of 30 in many AMOS programs.
AMOSmobile/EXEC
The AMOSmobile/EXEC usability has been improved and 2 new apps have been created -Customer Requirement Part Request and Work Step Classification.
A new app Customer Requirement Part Request has been introduced to request ad-hoc parts to perform customer requirement work.
A new app Work Step Classification has been introduced to classify work steps and to be aligned with AMOSdesktop.
AMOSmobile/STORES
2 new modules have been created - Return and Tools.
The return process consists of returning unused serviceable parts to store. This process is supported by AMOSdesktop and AMOSmobile/EXEC. With 22.12, a user can also return parts from AMOSmobile/STORES.
The status of the picking list is live updated, and the transaction is automatically reflected in AMOSdesktop if you are not offline.
At every step of the return process, you can use the bar code scanner without touching the screen.
The new Tools module displays all booked tools in the store with a counter. You can scan or manually select filters and an Undo function has also been added.
You can search for:
- booked tools
- expired tools
- tools booked for a specific user
- a usage
Material Management
The new Transfer Order layout shows all relevant information on one single screen. The extended drop down views of the header section display all the fields that were previously available in the legacy view. The colour coding gives a clear visibility of the order state and when you select the detail you can also clearly see the layouts of the tiles.
Engineering
Electronic Work Instruction (EWI) has been improved with additional options.
You can now define different default Next due Calculation Strategy applicable for View/Edit Modifications, Publication Management, Check Control System, Maintenance Programs Administration and Part Requirements Administration.
Planning
New Capacity Planning options have been implemented and harmonised through the different impacted programs.
Production
Component Booking is now release candidate and has been enhanced.
The interface has been adjusted to be more user friendly and intuitive.
Component Maintenance
Many options have been implemented and improved in Component Workpackage and Component Planning to fulfill the requirements.
- Additional filters
- A warning with the date of the linked customer repair order (RC) to compare with the start date of the workpackage
- New actions depending on the workpackage status (to be defined in Workpackage Configuration)
- A history of confirm shop arrival and route to next shop with a Show History button
- A new state column with icons for a better view of missing component and component sent to repair
- The possibility to create findings at the work step level and findings shopcards from a work template
- A new Workscope tab in order to prepare the next shop visits by assigning CAMO requirements to the workpackage before the component is removed from the aircraft
- The possibility to link a material production order (MP) created in Order Management to the component workpackage
- A Start Inspection action in the Release>Certification tab allowing to follow the component inspection and report back the requirements or modifications performed during the shop visit